Wykonywanie prac protetycznych na metalu z pozycji implantu metodą hybrydową
Mając na uwadze względy estetyczne, komfort psychiczny, zdrowie pacjenta oraz „żywotność” prac protetycznych, prace takie powinny być przygotowywane indywidualnie. Najważniejszym elementem jest łącznik indywidualny (belka/most z pozycji implantu). Problemem jest fakt, że takie łączniki są stosunkowo drogie, a używając klasycznych metod wytwarzania redukcja kosztów produkcji takiego łącznika czy mostu jest bardzo trudna.
Postanowiliśmy wyjść naprzeciw wymaganiom rynku i pochylić się nad znalezieniem sposobu na zmniejszenie kosztów wytwarzania wspomnianych wyżej elementów. Cały proces produkcji rozłożyliśmy na czynniki pierwsze. Czynnik, który najbardziej wpływa na koszt łącznika to koszt materiału: premilla lub krążka. Można poszukać tańszego dostawcy, ale często w parze z ceną idzie jakość. Nie jest tajemnicą, że każda obróbka ubytkowa generuje duże koszty związane z materiałem. Duża część tego materiału jest po prostu odpadem, więc płacimy za coś co później wyrzucamy.
Musieliśmy podejść do tego zagadnienia trochę z innej strony. Wzięliśmy pod uwagę możliwość użycia technologii przyrostowych. Najodpowiedniejszą technologią wydaje się być selektywne spiekanie proszków metali wiązką lasera (SLM). Dzięki takiemu rozwiązaniu koszt materiału jest ułamkiem kosztów materiałów potrzebnych przy frezowaniu. Należy jednak pamiętać, że drukowanie nie będzie tak precyzyjne jak frezowanie, co w przypadku zwykłych podbudów bez połączenia z implantem nie ma znaczenia. Natomiast połączenia implantologiczne muszą być wykonane precyzyjnie. Dodatkowo tytan jest łatwopalny, dlatego drukarki do spieku tytanu są zupełnie inne niż te do spieku chromokobaltu.
Pojawia się pytanie, czy jest jakakolwiek możliwość połączenia zalet tych dwóch technologii? Odpowiedź brzmi: tak. Dzięki naszej współpracy z producentami frezarki i drukarki oraz software’u CAMowego używanego do obu tych urządzeń, finalnie stworzyliśmy cały hybrydowy proces, dzięki któremu koszt łącznika jest niższy, ale jakość pozostaje niezmienna.
Cały proces jest stosunkowo prosty. Po otrzymaniu pracy w postaci pliku.stl, wgrywamy go do programu CAM i pozycjonujemy w przestrzeni roboczej drukarki dodając specjalne konektory. Przeliczamy projekt i wgrywamy do oprogramowania sterującego drukarką. Po wydrukowaniu pracy i usunięciu podpór, jest ona przenoszona do frezarki, gdzie montowana jest w specjalnie przygotowanej ramce „łapiąc ją” za wydrukowane wcześniej konektory. Wgrywamy położenie i kształt wydrukowanej pracy bezpośrednio w programie CAM pracującym z frezarką, ustalamy ostateczną geometrię połączenia implantologicznego, wybieramy odpowiednią strategię frezowania i przeliczamy projekt. Włączamy proces frezowania i szlifujemy wybrane elementy. Z reguły są to: połączenie implantologiczne, część poniżej profilu wyłaniania, kanał śrubowy.
Ostatnią i najważniejszą czynnością jest kontrola jakości wyprodukowanego elementu. Żadna praca nie spełniająca zaostrzonych standardów nie może opuścić laboratorium. Każda praca spełniająca standardy jest oznaczona numerem seryjnym i objęta gwarancją.
Jakość wykonywanych przez nas prac można spokojnie porównać do jakości prac uzyskanych w wyniku frezowania z prefabrykatów. Dodatkowo standardy kontroli jakości i ogólnie standardy wytwarzanych przez nas prac spełniają wszystkie standardy PCA w kwestii wytwarzania produktów medycznych.
Materiał został przygotowany na podstawie doświadczeń zebranych w czasie prac związanych z projektem „Modułowy, zintegrowany system do wielowymiarowego i wieloprzestrzennego projektowania wstecznego z hybrydową, indywidualnie dopasowaną linią technologiczną do produkcji elementów chirurgicznych w metodach przyrostowych” w ramach REGIONALNEGO PROGRAMU OPERACYJNEGO WOJEWÓDZTWA ŚWIĘTOKRZYSKIEGO NA LATA 2014‑2020 realizowanego przez DentalHolding Sp.z o.o. we współpracy z Politechniką Krakowską.
Wykonywanie prac protetycznych na metalu z pozycji implantu metodą hybrydową
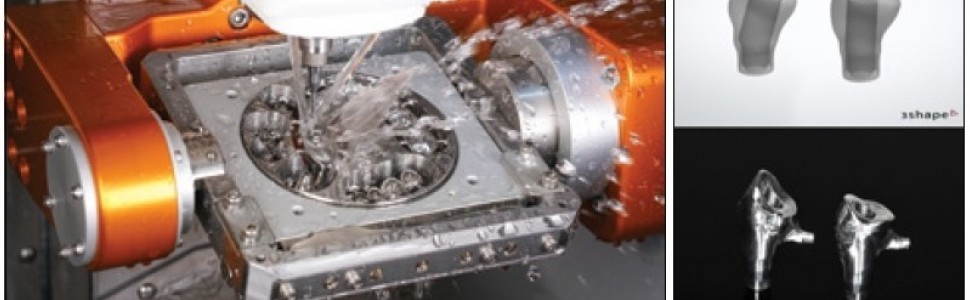
MS 2020; 11: 69.
m